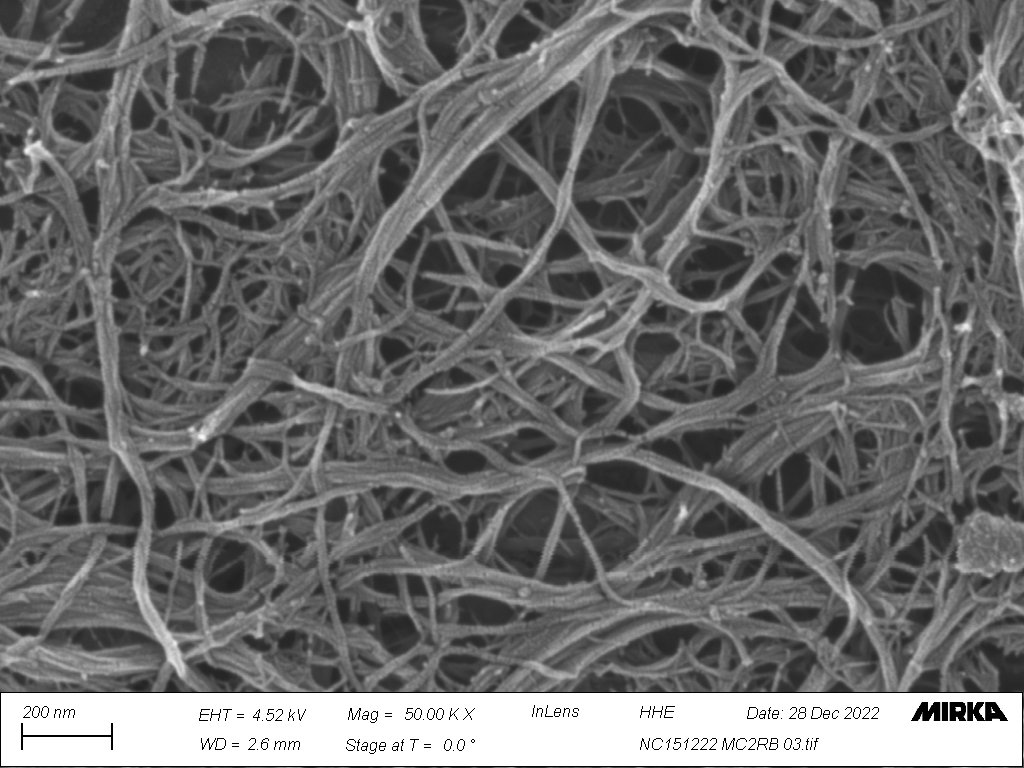
HydBondCell project envisioned to develop novel filter materials by unlocking the potential of controlling the hydrogen bonding of cellulose structures
ProjectsThe HydBondCell project (Control of hydrogen bond formation in cellulose structures - one application area a biomaterial-based filter membrane) was a two-year Business Finland funded project that officially came to its close in January 2024. The project consortium, led by Tampere University (TAU), comprised of six partner companies covering the whole value chain ranging from equipment and raw material suppliers to filter membrane manufacturers. The project set to tackle the growing demand for more sustainable and bio-based raw materials for filter membranes by utilising the largely untapped potential of nano- and microfibrillated cellulose.
Main photo shows Microfibrillated birch pulp.
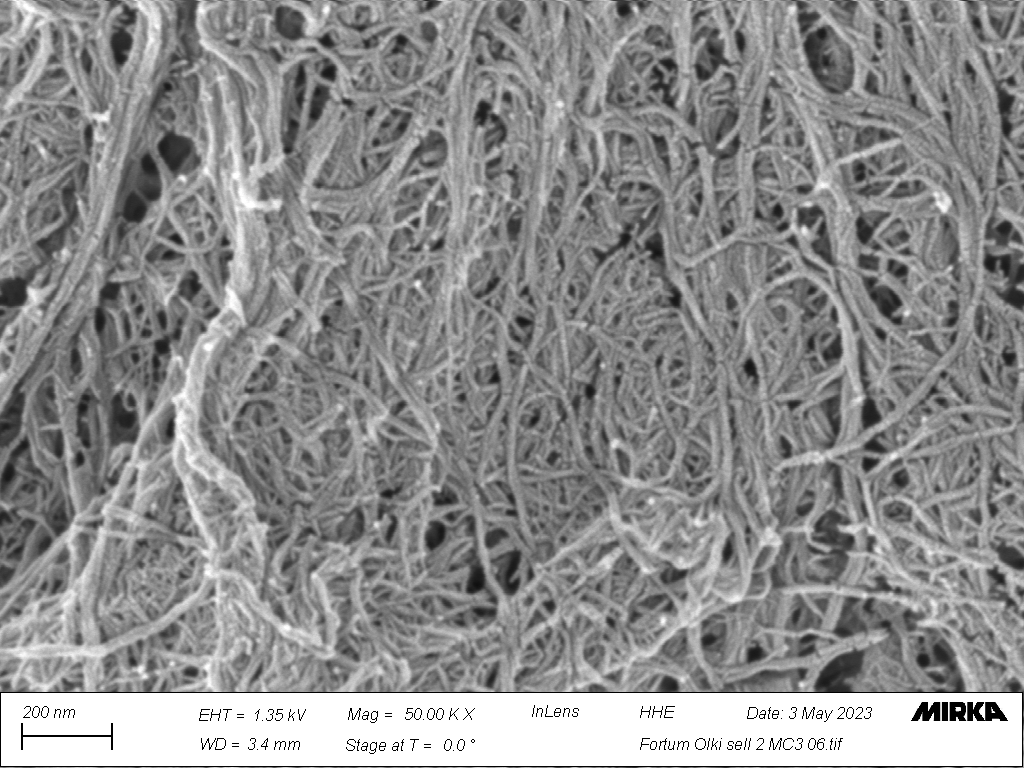
Image: Microfibrillated straw pulp.
ExpandFibre team was delighted to invite key stakeholders of the HydBondCell consortium to discuss the project and to reflect on the project’s main outcomes. Project coordinator Tomas Björkqvist, Senior Research Fellow at Tampere University was joined by Juha Kariluoto, CEO at Eagle Filters Oy, and Petter Andersson, Project Engineer R&D at Mirka Oy, to look back at the collaboration that kicked off in September 2021.
Background to the HydBondCell project
Tomas wanted to offer a glimpse into the path that led to the creation of the project: “In my previous research work, I had already been working with the topic of cellulose microfibrillation for years prior to starting the HydBondCell project. In my previous work I had noticed that without significant modifications to the commonly used microfibrillation equipment, it would be challenging to successfully industrialise the manufacturing of fibrillated or broken-down cellulose fractions such as microfibrillated cellulose or nanocellulose – materials which had a lot of potential for various end uses due to their unique properties. Simultaneously I had also established a connection with Mirka, where Hans Hede, Development Engineer R&D, had developed a special equipment titled Polymill 1 for mixing polymers and dried powder-form ingredients with liquid adhesives to be used for Mirka’s own industrial processes. This kicked off a fruitful collaboration between TAU and Mirka where TAU offered the process principles and Polymill 1 was adapted also for microfibrillation, continuing also into the HydBondCell project. In parallel to the project, we designed a completely new microfibrillator model titled Polymill 2 producing highly uniform microfibrillated fractions with up to 50% lower energy consumption to state-of-the-art equipment.”
Petter continued: “We at Mirka have had a strong role in the designing and building of the microfibrillator, and the process optimisation work is still ongoing. As we are not a filter material manufacturer as such, we are of course very happy to explore additional potential application areas for the equipment we have designed together with our partners.”
Nanocellulose and its variants have been widely recognised as a potentially revolutionary product family for the global forest industry already for years, as explained by Tomas: “Nanocellulose is still researched widely all over the world, but in my opinion more emphasis should be placed on finding more economically feasible manufacturing methods for it. Various companies use different technologies to manufacture microfibrillated cellulose at varying scales using different fibrillation processes and for example microfluidization. There has also been interest to use microfibrillated cellulose directly for producing wood-based textile fibres without the use of solvents. Japan is the leading developer of nanocellulose materials in Asia, but the processes used in Japan commonly use very harsh chemicals for pulp pre-treatment, which we want to completely avoid.”
Key outcomes of the project
From a purely research point of view the outcomes of the HydBondCell project can be divided into two specific areas as detailed by Tomas: “The main learning from the first part of the project – mechanical production of nanocellulose from straw and wood pulps – was that even in the thin plate gap fibrillator the pulp did not gradually get thinner, but merely opened up to fibrils or remained as intact pulp fibers or as large fragments of a pulp fiber. This was further revealed by e.g. scanning electron microscopy (SEM) images. When gradually tightening the gap in the fibrillator, also majority of the tougher fibers opened up to fibrils. The nanocellulose that we produced from both straw and birch pulp was down to 5 nm in width, which is a finer material than the most advanced fossil-based fiber materials, that are used in filters today. In theory, this would allow the production of nanocellulose-based filter materials with high filter grade and low pressure drop.”
Tomas continued: “The main learning from the second part of the project – production of filter materials from nanocellulose – was that the controlled placing of nanoscale cellulose remains challenging due to the different forces acting in the nanometre range. The effect of the dominant hydrogen bond formation could be partly hindered by changing the commonly used water media to isopropyl alcohol (IPA) before drying of the filter material structures. Even with the decreased hydrogen bond formation, it’s challenging to influence the creation of nanocellulose based filter materials with both high filter grade and low pressure drop at high gas flow, which are also feasible to upscale towards industrial production. Thus, there is still plenty of work to be done for this topic in the future.”
The project also had outcomes for the industrial partners as explained by Petter: “Abrasives, sanding tools and polishing compounds are our main focus at Mirka. Regarding the work carried out during the HydBondCell project, we would be interested to pursue the development of hardware, including friction surfaces and grinding stones, for the fibrillation of cellulosic materials and other relevant applications.”
Juha opened the topic from the point of view of a filter manufacturer Eagle Filters: “Our main goal in the project was to develop a bio-based filter membrane. We trialled various coating technologies, for example, and used our own electrospinning pilot machinery extensively. Despite the thorough work carried out during the project we were unable to reach the desired end result with optimal filtering properties. In general, we’re always interested to pursue finding new bio-based raw material options for filter membranes, which are also biodegradable. Thus, we were very happy that we could take part in the project.”
Looking ahead to the future
Petter continued on the immediate future plans of Mirka: “COCOBIN project, also part of the ExpandFibre Ecosystem, has started earlier in 2024, and we’re happy to continue exploring the topic of nanocellulose within COCOBIN.”
Tomas continued: ”Although the research for the HydBondCell project ended in January 2024, we have been ideating on a novel coating method, which aims at successfully creating uniform nanocellulose layers on top of a sparse substrate. Creating uniform structures with nanocellulose is a fundamental challenge as nanoscale particles tend to self-assemble in ways that are very hard to predict. For cellulosic materials hydrogen bonding is one of these primary forces. In principle, we would need to create structures where the blank spaces between the fibrils are small enough to leave the particles on the filter membrane but let the gases pass through. Transferring the research into industrial scale remains a central challenge for us to still tackle in the future.“
According to the three interviewees, it’s clear that the demand for bio-based and biodegradable filter membranes is significant globally with the commercially available options being largely based on fossil-based raw materials such as polyester (PET) and polypropylene (PP). Most likely there will be new initiatives trying to unlock the vast potential of nanocellulose by solving the inherent challenges posed by its nanoscale size.
Photo credit: HydBondCell
HydBondCell project fact sheet
Project budget: 350k€, Business Finland Partnership model
Project duration: September 2021 – January 2024
Project partners: Tampere University (coordinator), Fortum, Mirka, Valmet, Filterpak, Eagle Filters, and Nanoksi